Fujifilm Europe has installed five wind turbines at its manufacturing and R&D site in Tilburg, The Netherlands. The five Vestas V90 wind turbines, each able to generate a maximum of two megawatts, are capable of generating approximately 20% of the total energy used by the 63 hectare Tilburg site. This development is part of an ambitious target set by FUJIFILM Manufacturing Europe B.V. to become a carbon neutral site, with the wind turbines alone likely to reduce CO2 emissions by 12,000 tonnes per year.
The company has also installed a water recycling facility, consisting of two large water purification units, on site. With these and other sustainability measures in place, FUJIFILM Manufacturing Europe B.V. estimates that it currently reuses 13% of the waste it produces, recycles 68%, regenerates 18% and so is left with less than 1% of the total site waste to dispose of.
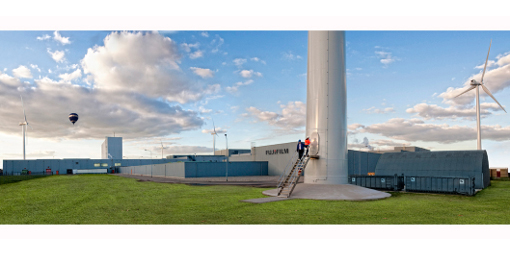
To supplement these initiatives, however, Fujifilm is also investigating the possibility of cleaning some of the waste water the site generates for reuse within the production process, as well as the option of constructing a complete waste water treatment system on site, in collaboration with three neighbouring companies. In addition, a feasibility study is also in progress for replacing the natural gas used in production with bio-gas, with the results of this study due to be available at the end of 2011.
Ryuta Masui, senior vice president, FUJIFILM Europe GmbH, comments, “Fujifilm has always been committed to the environment as we feel that we have a responsibility to reduce our burden on the planet as much as possible. With the last of our five windmills now in production, we are proud to be able to generate 20% of the energy we consume at our Tilburg manufacturing site through wind power.”
He continues, “It’s not only the way in which we manufacture our products that is important but also the products themselves. We aim to manufacture both processless and low-chemistry offset plates at this site, and are also in the process of developing other exciting products for sustainable applications in other areas of our business here at Tilburg.”
The company is also pleased to confirm that its highly anticipated third state-of-the-art offset plate manufacturing line (PS-10) is close to completion, as originally announced. The new PS-10 line has been designed to be able to manufacture Fujifilm’s ‘lo-chem’ family of plates, alongside Fujifilm’s most advanced printing plate to date, the recently launched Brillia HD PRO-T3. Once complete, these investments will not only make Fujifilm’s plate production facilities in Tilburg one of the largest in the world, but also the most sustainable.